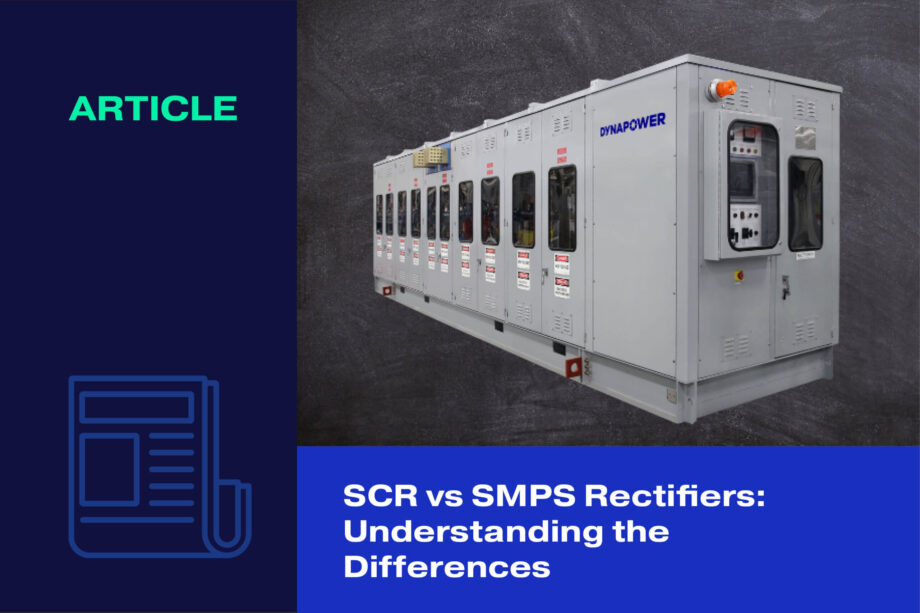
Two major considerations when deciding what type of rectifier to purchase are the cost and ease of maintenance. With regard to SCR vs SMPS rectifiers, their ultimate differences and similarities may surprise you. But first, let’s discuss the key characteristics of each of these rectifiers.
What is an SCR or Thyristor Rectifier?
An SCR or silicon-controlled rectifier is a semiconductor device that can be used to control electricity by turning on and allowing power to flow through it. Typically 6 of these devices work together to rectify electricity in a 3 phase industrial rectifier. Typically the longer the SCR is open, the higher the voltage leaving the rectifier.
SCRs are variable voltage DC power supplies that are low frequency, high ripple systems. These systems are rugged and have a history of high durability – a number of our customers have systems running after 40 or even 50 years. They regulate and react steadily, carry a lot of power in big copper windings, and are fairly easy to troubleshoot with large, easy-to-identify components.
Most of these designs have an ANSI number associated with them, meaning that the design is electrically consistent across manufacturers. You can see the same build from one brand of power supply to another.
What is an SMPS or Switchmode Power Supply?
An SMPS or switch mode power supply by comparison is a relative new kid on the block. Commonly called switchmodes, these devices are electronic power supplies that convert electrical power from one voltage to another with high efficiency and in a compact design. They switch from AC to DC, back to AC, then once again back to DC. Since the process is all done at high frequency, the internal parts can be smaller thus the entire unite is smaller. They utilize a high primary voltage—the 480VAC input unit to the unit is rectifier into capacitors at 650-700VDC—and is used to power the IGBT primary winding circuit on the transformer.
With smaller parts, tighter windings, smaller footprints and an even tinier tolerance, these precision pieces of equipment offer good space efficiency per watt, modern computer interfaces, and intuitive controls.
Actually switch modes aren’t all that new – they have been around for almost 40 years and were traditionally used in smaller current applications. Large-scale switchmodes weren’t deployed until around roughly 10-15 years ago. Today, this technology has become much more widely used due to the rise of quality, precise manufacturing processes and trade globalization.
SMPS vs SCR: The Basics
Before getting more granular on each type of rectifier, let me dispel a popular myth regarding SMPS vs SCR: Neither unit is better than the other. Both SMPSs and SCRs perform identically well in electronic regulation, and technology and manufacturing techniques have allowed them to perform to the same level of process performance. SMPS and SCR devices can both regulate to the 10th of a volt and even more, there is absolutely zero difference between them in their ability to withstand exposure to corrosive process chemicals. Environmental degradation for rectifiers is a critical consideration that, unfortunately, many facilities overlook.
Repairs
Looking at total repair costs coupled with chemical exposure over the lifetime of both SMPS and SCR rectifiers, the investments with either rectifier are within 1 percent of each other (this figure is based on customer feedback over the last several years, in the U.S. market, across 13 different rectifier manufacturers.)
Regarding repair scope, the fix is often the same principle whether it’s SCR rectifiers or rectifiers used for welding. Whether you have to change a single SCR component worth $700 once in 15 years or you have to change ten $70 diodes in batches of five, twice in 10 years, the equipment repair cost is similar. In fact evaluations in lifetime repair costs measured by rectifier type or design vary greater in brand manufacturers than they do between design types within one manufacturer.
What does change depending on the rectifier is the frequency and manpower that goes into the repairs: more repairs with less costly parts, or fewer repairs with more expensive parts. Until you factor downtime on the line into the equation, the costs incurred through manpower and parts combined are very similar. Even if you factor more frequent breakdowns into the equation, switchmodes have the ability to swap entire rectifiers in a few hours, unlocking another maintenance option that SCR units don’t easily access. Ultimately, both SMPS and SCR rectifiers are equally susceptible to the environment and when you compare the systems cost-wise, they are almost identical in the rate of degradation per dollar to fix it.
So, the main questions you should be asking yourself when considering SMPS vs SCR rectifiers are:
- What real estate do you have to install and service the rectifier(s)?
- What kind of upkeep do you have the manpower and time to commit to?
- What kind of chemicals will the rectifier(s) be exposed to?
- What is the flexibility in terms of being able to maintain and work on your rectifier(s)?
- What is your process and line design and does it match what the surrounding production facility requires?
SMPS vs SCR: Diving Deeper
What are key considerations for each type of rectifier and its performance?
- Switch modes are physically smaller, will take up less real estate, offer lower consumption of cooling resources, and tend to—on average—perform the full range of operation at a higher electrical efficiency than SCR rectifiers.
- Switch modes run at higher frequency allowing a tighter configuration and smaller weight while delivering the same overall power as an SCR rectifier. However, those smaller components tend to fail more frequently than the larger SCR componentry due to relative size when exposed to chemicals or moisture.
- The more you decrease the voltage in an SCR rectifier, the higher chance the machine will not convert AC to DC as efficiently as the same rated, competing switch mode. However, the more you increase the voltage in an SCR rectifier, the better chance it has of performing more efficiently than the same rated, performing switch modes.
- Because it takes more switch mode units to match the regular output amperage of an SCR, with switch modes you will have more points of potential failure as proven in the Weibull Analysis—which is a methodology used to determine reliability characteristics from field or laboratory test data.
- The rate at which both SCR and SMPS rectifiers break down is much more dependent on environmental factors than in how the rectifier is used or the time that the machine is exposed to the environment. In fact, 93% of rectifier repairs are the result of environmental hazards vs. equipment misuse (i.e., rack crashes, improper setpoints, or chemistry exposure).
The Importance of Quality Cabinet Design
Equipment that is going to last for the long haul always starts with a good cabinet. If you can manage where chemicals go—i.e., if you can control the environmental exposure—while still effectively cooling the equipment, you are ahead of the game. When air cooling, the rectifier pulls air which will enter wherever it can – and with it, comes chemicals that will invade and begin destroying your equipment. A cabinet rated NEMA 1, which essentially just offers light-duty door panels, may not do enough to keep the chemicals out.
That’s why when evaluating any type of rectifier, it’s critical to realize that not all cabinets are rated the same (NEMA 1 vs NEMA 2 etc.) or created equal. Quality rectifier cabinets use gasketed air paths and pull the environment’s ambient air used through a designated heat sink channel for cooling, thus avoiding contamination and internal damage.
Rectifier design can also help protect the internal electronics. For instance, if a rectifier has all its components mounted on the opposite side of that heat sink channel, then they won’t be exposed to outside ambient air. In such a case, the rectifier will keep running as long as the heat sink barrier remains in place between the rectifier components and the potentially hazardous ambient environment. Basically, you’re choosing the heat sink to be the sacrificial component of your rectifier over the actual electrical components, which works because the heat sink is designed for protection and controlled exposure.
Key Considerations in your Facility
Chemicals / Environment
What environmental hazards does your facility have? It’s important to know the chemicals being used in your processes. For instance, if you use hydrochloric, sulfuric, nitric, or hydrofluoric acids — a chemical family typically used in acid etching and surface prep for plating, painting, or power coating—you need to understand that acids destroy aluminum and copper.
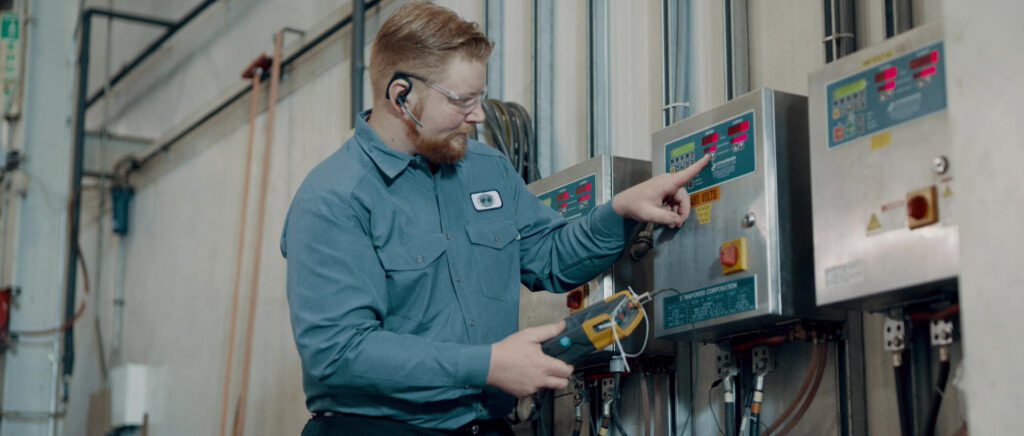
So, if you install a new air-cooled rectifier, the heat sink and bussing will get chewed up in 6 to 8 months. Instead, consider a water-cooled NEMA 4X or IP56 fully sealed rectifier as your best bet.
Real Estate
Stocking spare parts will allow a maintenance issue to be quickly taken care of and allow your production to continue with minimal interruption. Consideration of spare parts is another place we see significant differences between SCRs and SMPSs. Individual SCR parts are large, heavy, costly, and can be subject to long lead times (based on market trends). Individual SMPS parts are smaller, less expensive, and easier to store due to their size – but that also makes them easier to misplace. Some rectifier manufacturers don’t offer the option to replace individual parts and require replacement of whole modules. In this case, then, both rectifiers score about the same in terms of space and budget. But if individual parts can be replaced, and if your space and budget for spares are limited, it may make more sense to consider an SMPS. It has nothing to do with one being better than the other, it’s just another consideration to have in mind as you spec your rectifier.
SMPSs vs SCRs have very different resource requirements.
- SCRs are more resource hungry both in footprint and real estate. They require strong weight-supporting platforms and wide installation spaces.
- Air cooled SCRs require room to allow forced air cooling to escape.
- Water cooled SCRs require discharge to be waste treated.
- To repair an SCR, there is no single point of access, so technicians need to be able to get three different angles to perform maintenance work on an SCR unit. If they can’t get into it, they can’t fix it if it breaks, so technicians need at least two feet around the unit so there is enough space to perform maintenance checks and complete repairs.
Maintenance
One thing that customers should be aware of when it comes to SMPSs is the learning curve involved with these systems. The equipment is much smaller and has tighter arc paths with larger voltage potentials inside. The opportunity for a breakdown is different, and the equipment follows a different preventative maintenance path to keep it running. Think of it like this: the maintenance requirements for your sportscar are quite different from those for your trusty diesel pickup truck. An SMPS is a different animal and it’s important that customers understand the units and their maintenance requirements.
Planning for maintenance is very important when searching for a new or refurbished SMPS or SCR. Don’t buy a rectifier without considering what it will take to service or perform maintenance – at Dynapower, we understand maintenance needs because we are highly expereinced aftermarket service providers. We know some other companies avoid talking about life cycle of their equipment because the longevity and serviceability just isn’t there. At Dynapower, we’re different: we support customers in servicing their equipment and work to educate them on how to do this – whether you have our equipment or not.
Dynapower: SMPS vs SCR Rectifiers
At Dynapower, our SCR and SMPS units are designed to be easily accessible and serviceable to reduce total cost of ownership. To make servicing even easier, we offer rectifier training classes with hands-on repair application, so your team becomes comfortable with working on each of the topographies of rectifiers offered in the market. Further supporting the self-service option is the fact that for SCR components, our documentation and record keeping go back 40 years and offer a level of detail that is second to none in the industry.
Dynapower switch modes offer some of the best long-term value in the industry. Fully 100 percent of the power electronics can be changed and replaced and trained technicians with a dedicated repair area can perform these repairs in the comfort of their own facility. And, most of our SCR equipment is designed to be serviceable without lifts or cranes for general repairs and maintenance. With competitors’ rectifiers, the focus is on cheaper upfront costs which may sound like a good deal. However, these units are not meant to be reparable – you end up trashing the entire unit and losing your whole investment. With Dynapower rectifiers, we can change out the internal components in our switch modes and you can have brand new power electronics without scrapping the case, interface, or controls—which makes us unique in the marketplace. It’s a quality unique to Dynapower’s equipment that saves our customers money each year they have it in operation