Rectifiers are pretty awesome pieces of equipment and can last decades before needing replacement. However, some rectifier components do not share a similarly long life expectancy. Circuit boards or semiconductors degrade as part of their natural lifecycle and will need to be replaced several times in the rectifier system’s lifetime. In fact, failing to replace these parts in time can cause numerous problems, some very serious, including:
- Loss of efficiency;
- Loss of communication capabilities;
- Loss of operator control;
- System failure;
- Injury or even death.
When these conditions arise, it’s critical to determine the source of the issue and outline the best plan of action to address it. There are several options of how to handle these issues. Customers can:
- Replace the entire rectifier regardless of the integrity of the core components
- Upgrade the controls and functionality at time of part obsolescence
- Refurbish the rectifier – cleaning and reassembling every square inch of the power supply, similar to detailing a car, refurbishing gives the unit that “new rectifier smell.”
- A key feature of microgrids is their ability to support the demand for independence and resiliency of the existing grid system. As we’ve repeatedly seen, our over-reliance on the existing power grid as well as the limitations of its aging infrastructure pose a substantial risk to the industrial, commercial, residential, and governmental sectors who need a steady and dependable supply of electricity.
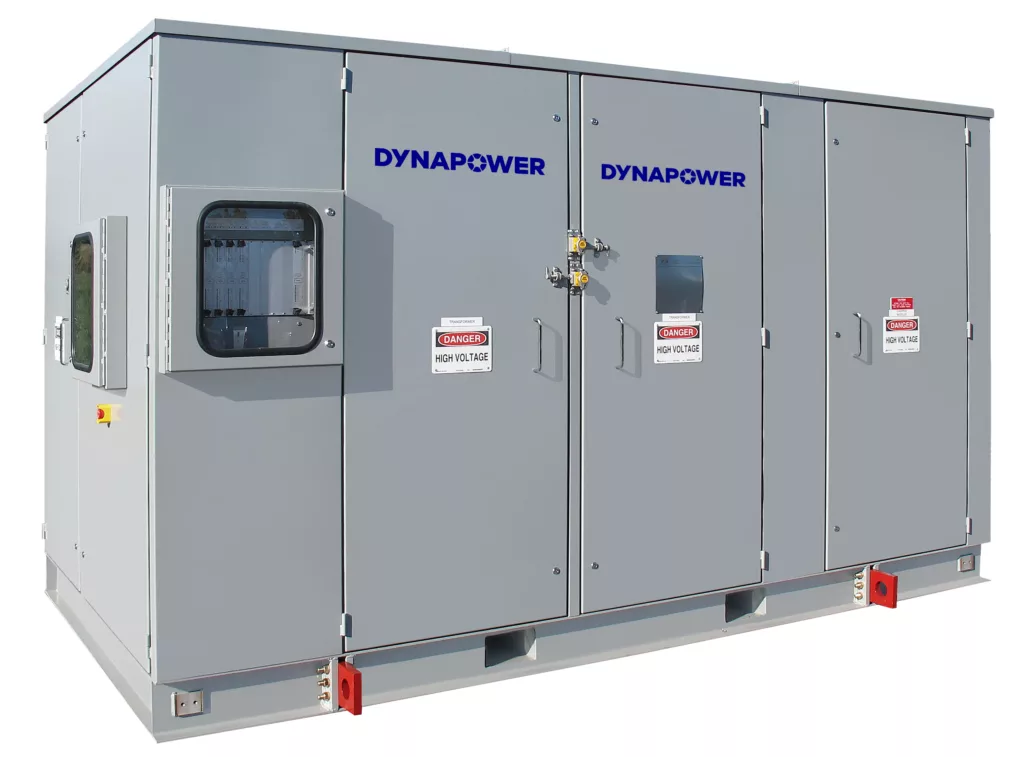
At Dynapower, we have a dedicated team of experts that can help you make that determination. We are proud to offer comprehensive remanufacturing services to refurbish any make or model rectifier, and a state-of-the-art and free on-site rectifier assessment program. Our program provides owners and maintenance teams with a detailed report of the health of each rectifier and priority-based maintenance recommendations to help increase the longevity of the system.
Why a rectifier refurbishment is likely the best solution
Our industry-leading service team is trained to service virtually all brands of rectifiers so you can take advantage of our rectifier services regardless of the brand of their unit. The primary benefits of refurbishing an existing rectifier include:
- Increased efficiency, safety, and reliability. These improvements are achieved while also saving 30% to 60% from buying new.
- Ease of use. Integrating more modern parts and controls will update the rectifier, allowing it to communicate with newer technology in your plant and become more connected where you need your data.
- Ease of staff training. As rectifiers go to be rebuilt, there can be some creative liberty taken in parts used, configuration, wiring, and design. This positively impacts your business with faster troubleshooting, easier PM maintenance, and more reliable methods of operations.
- Lessened impact to operations: Replacing a rectifier is a big job. Besides the downtime from the rectifier being offline, the physical requirements of replacement and the possible impact to infrastructure (rectifiers are big and might require changes to a facility layout) mean a rectifier replacement can impact your facility’s production schedule for weeks or more. Rectifier refurbishment can be largely coordinated ahead of time. The result? Measuring downtime just went from weeks to days.
- Standardized maintenance and replacement parts. Pick and choose your upgrade to accommodate your company’s spare parts inventory, training capabilities, quality requirements, or ease of troubleshooting. It is far easier to work on equipment that matches the machine next to it than having no reference. Plus, spare and replacement part inventory can be streamlined versus having to stock parts for multiple manufacturers’ units or generations of design.
- Extended equipment life. Modernizing the rectifier also helps to extend its service life. It also allows equipment to comply with today’s safety standards and codes, reducing hazards to employees.
- Smaller environmental impact. Choosing to refurbish existing equipment rather than scrapping it is a much greener alternative as it minimizes the amount of retired equipment waste, does not utilize resources to build new equipment, and allows systems to return to optimal performance, thus reducing energy usage.
Some customers purchase spare rectifiers to ensure that they never experience system outages. To facilitate these situations, they can refurbish an old rectifier to keep as a backup. Or we can build a new rectifier to start, provide high amp cables to allow for easier hookup, and have a technician on site to help swap out the old rectifier to minimize downtime.
Dynapower’s on-site rectifier assessment program
Choosing to use our on-site rectifier assessment program brings our Dynapower team to your facility to perform diagnostic testing. Following the testing, we provide a detailed report of each rectifier’s health, as well as priority-based recommendations for maintenance.
More specialized testing procedures are available in-house with our industry-leading test equipment. In these situations, we use return merchandise authorization (RMA) to ship the unit to our facility for testing.
Our focus is always on customer satisfaction, so we ensure that we are meeting your preferences at every stage and outline all suggested work and deliverables. Most importantly, before a refurbished rectifier leaves the facility, it is tested to ensure it meets the standards of a new rectifier. Complete documentation of these tests can be provided to corroborate the refurbished rectifier’s quality. The test reports also double as a reference for repairs and quarterly maintenance checkups your technicians will perform during a normal PM cycle.
Contact Dynapower for quality rectifier services
Dynapower is an industry leading rectifier manufacturer and aftermarket service provider. We can repair, upgrade or replace any outdated equipment and provide a cost-efficient and green solution that will increase the performance and longevity of your process. We offer spare parts, on-site repairs, preventative maintenance, employee training, and free, 24/7 technical support services from a team of dedicated professionals.