Behind The Power:
Alan Davis, Technical Support Specialist
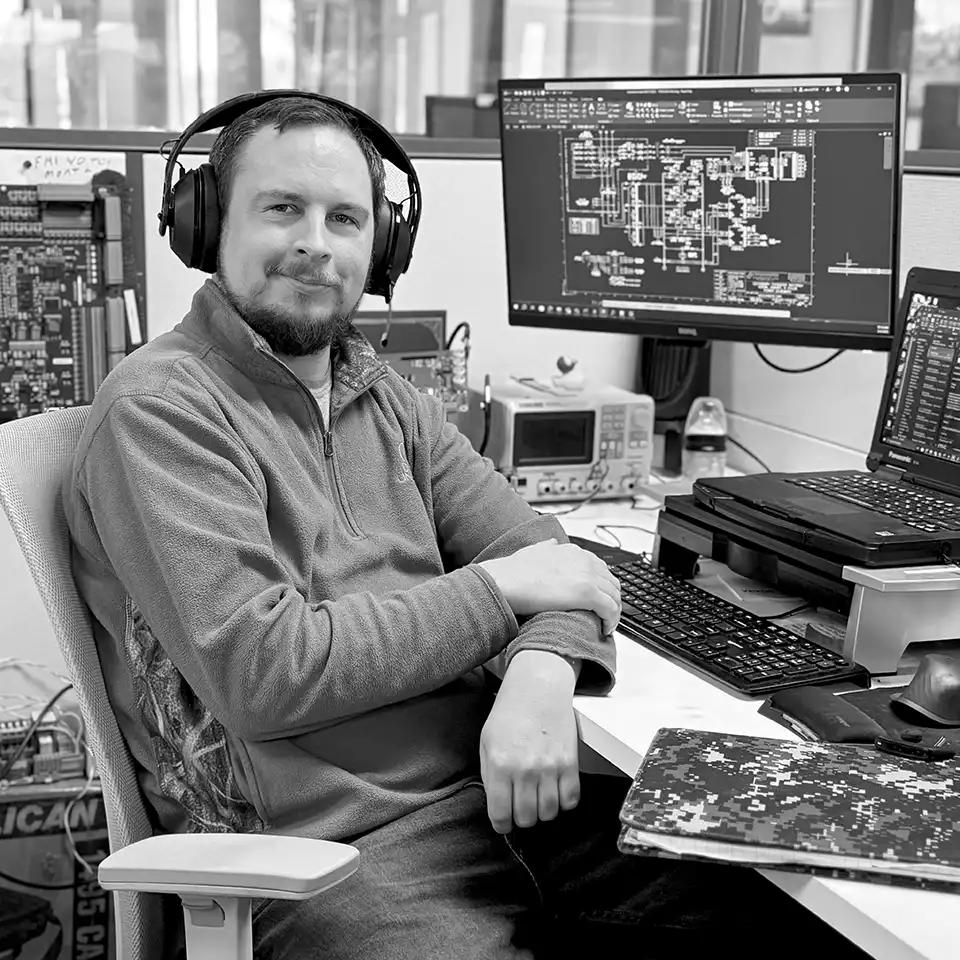
The joy of restoring power to critical systems
By troubleshooting complex equipment issues for customers worldwide, Alan often guides users remotely through diagnostic procedures across diverse industries ranging from manufacturing to utility-scale clean energy to food production.
Q: What do you like best about your job?
A: Well, a couple of things. First, I get to interact with people from across the world and help them on some of their roughest days, trying to fix things that aren’t working, then drastically improve their day when we get them running again. The second thing is that I get to see what our equipment does in a wide variety of industries—from simple things like making screws, to chemical production, to building fighter planes… and even the making of soy sauce. I enjoy the added challenge of troubleshooting over the phone because I can’t put my hands on the machine. I have to guide another person who may or may not know much about their machine, picture it in my head, and determine whether that machine is actually broken, or maybe some training needs to happen instead.
Q: What words would you use to describe the company culture?
A: Well, the biggest one is ‘family’. This is a very unique organization in that most of us know and can depend on one another. Another one is ‘helpful.’ If I have a problem with a machine out in the field, I know I can talk to my engineers. I often know exactly which engineer will have the answer I need, and most of them will take the time to answer my questions. The third is ‘passionate.’ Dynapower’s people are passionate about what we do, especially those who understand what impacts our equipment have on the world around us.
Q: In what ways do you influence the quality of the products here at Dynapower?
A: I have a very big role in that. Any issue with our equipment in the field usually comes through me first. I take the information from our service technicians and customers, and even from tech support lines or parts requests. If I see trends with a product line, I raise concerns with engineering. Then we can start working on solutions. I get to be the bridge between the rest of the world and our product development teams to drive continuous improvement in what has left the building, what’s still here, and what still has to come out.
Q: What is something you do in your job that is innovative?
A: For me, it’s in helping the customers and our technicians troubleshoot problems and find solutions. The part where innovation comes in is when I coach people through finding alternative solutions to a problem. I get to be that second set of eyes that might see a different pattern and find a solution or find the right people to help. All this ties back to quality as I find ways to improve our product lines.
Q: What are some ways that you continue learning in your field?
A: One thing I love about this job is I never stop learning. I’m constantly learning about how our machines work and how customer processes work, because we don’t just fix power supplies— we have to understand what our power supplies are being used for. I have to understand chemical processes like electroplating, anodizing, or color anodizing (where you have one power supply that can create an entire palette of colors just based on how you shape the voltage coming in and out of that machine), or any number of other neat processes and applications.
Q: What do you like to do for fun?
A: Right now, my biggest hobby is photography. It has been giving me an excuse to get out, get exercise, and take pictures of all kinds of things. It encourages me to appreciate beauty in the everyday, mundane things around us. My second biggest hobby is playing airsoft, as it gets the blood pumping, adrenaline rushing, and you can visualize stress leaving your body laterally at high speed in a completely legal, fun, and constructive manner.
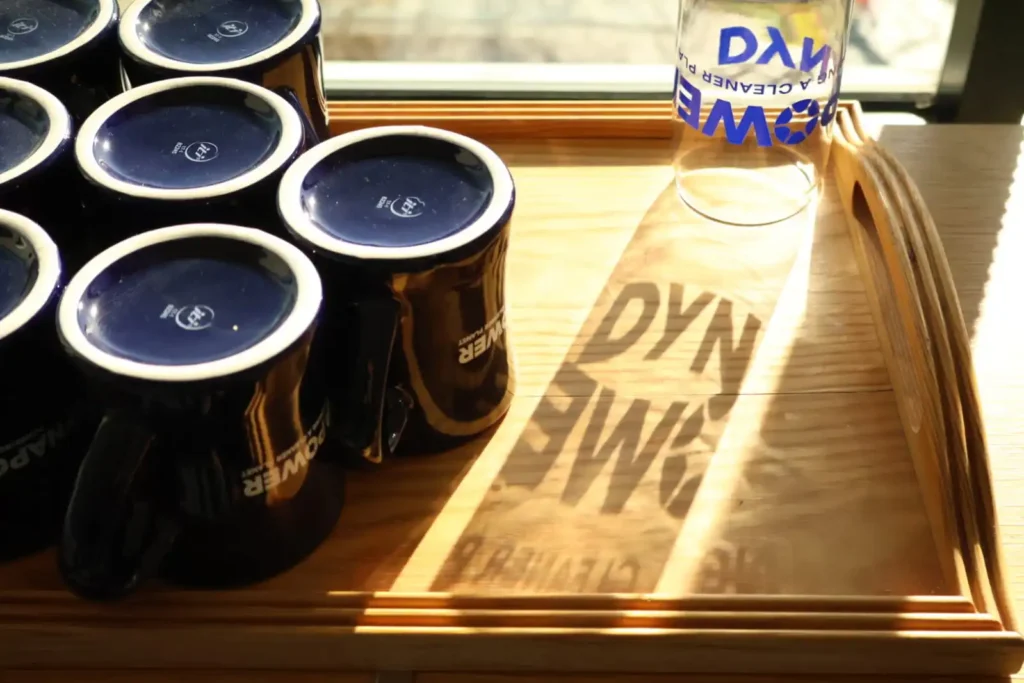
Photo by Alan Davis
Leave a Reply